在国家大力推进智能制造的背景下,引进自动化生产模式、推进数字化建设是企业转型的必经之路。近年来,万生人和模塑部聚焦以创新驱动发展,有计划地对医疗器械生产线的生产设备和工艺流程进行升级和优化,进一步提高生产制造水平,加大产线自动化投入,助力企业提质增效。
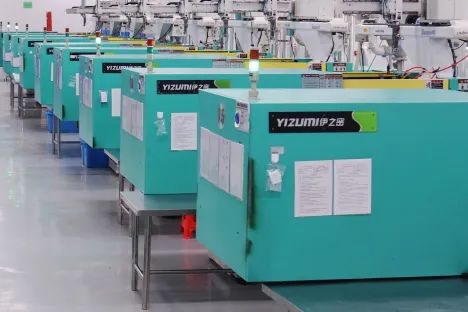

模具结构“新”,技术攻关降成本
模塑部自组建以来,大力推行技术创新管理理念,专注于医疗器械配件的批量快速生产。通过逐一梳理分析生产工序,比对生产数据,瞄准生产瓶颈点和低效环节,持续优化生产流程。
以吸氧管产品为例,发现注塑工序生产的配件存在毛刺、瓶体偏芯等问题,进而导致产品需人工二次加工后再转入下道工序。为提高生产效率,模塑技术小组反复研究,决定从模具结构入手,为湿化伞加装针阀式热流道、瓶盖模具加装气缸,有效消除了毛刺。同时,利用自主创新矫正技术,解决了瓶体模具偏芯难题。经过持续试验和优化,注塑工序减少了人为加工、检验等繁琐环节,人员配置重新调整;生产的产品也实现一次达标,成功缩短了产品生产周期,有效降低了生产总成本。此次创新举措标志着生产车间在自动化生产的征途上迈出坚实的一步。
制造过程“新”,持续优化提效率
标准化是自动化的基础。要实现生产车间自动化,模塑部首选做好工艺、流程的标准化,对生产工艺进行全面梳理评估和大量的基础数据调研,制定标准工艺操作流程,确保生产过程的一致性和可控性。
立足工艺创新,模塑部在设备升级方面也采取了各种创新举措,将车间冷却循环水系统改为集中制冷循环,显著提高了冷却效率,减少了设备停机时间;优化组装工装结构,进一步提高生产效率;同时,研制新型取出工装、改进机械手治具、减少半自动作业工序,引入色母机、中央供料系统等系列自动化设备,实现了车间自动配料、自动输送等技术,大幅降低对操作人员的依赖,生产效率整体提升了20%。
生产设备“新”,自主研制促生产
自动化生产线可引入智能检测设备实现对产品的质量控制,减少人工干预,提升产品质量稳定性。然而,由于公司产品形状特性及半透明材质,市面上现有的设备往往难以达到质量检测要求,或设备价格过高。面对困局,模塑部联合研发部门在2024年初成立项目组,自行研究、制造视觉检测设备。
项目组成员充分发挥各自优势,协同工作,从分析制作原理、软件算法、机械结构等方面入手,成功装配出检测样机。经过无数次的调试与优化,逐步解决拍摄像素不清晰、光源不均匀等问题,最终提升了设备性能。目前,样机已进入整体测试阶段,预计下半年正式投入使用。设备制作成本仅一万多元,与市面上功能相似的设备相比,节省了160余万元。基于公司需求与生产实际,模塑部以项目组形式完成了自动换箱设备改造、导水芯自动化组装机制作等多项技术改进创新成果,为企业“高效低耗”的可持续发展道路奠定强有力的技术基础。
自动化的推进不仅顺应了当前制造业转型升级的发展趋势,也成为提高企业竞争力的重要手段。下一阶段,模塑部团队将继续加强相关技术研究和培训,不断推进技术和管理创新,以适应数字化时代的需求和挑战,推动企业高质量发展。